FMEA vs FMECA
Begge, FMEA og FMECA, er to metoder som brukes i produksjonsprosessen, og det grunnleggende faktum i forskjellen mellom FMEA og FMECA er at den ene er utvidelsen av den andre. For ytterligere å forklare, er Feilmodus og Effektanalyse (FMEA) og Feilmodus, Effekter og Kritikalitetsanalyse (FMECA) to typer teknikker som brukes til å identifisere spesifikke feil eller feil i et produkt eller en prosess, og å ta korrigerende tiltak for å rette opp problemer; og FMECA er en utvikling for FMEA. Denne artikkelen presenterer deg en videre analyse av forskjellen mellom FMEA og FMECA.
Hva er FMEA?
FMEA står for Failure Modes and Effects Analysis, og det kan betraktes som en trinnvis tilnærming for å fastslå feil eller feil som oppstår i produksjons-, design- eller monteringsprosesser eller i produktene eller tjenestene.
Feilmodus betyr modusene eller måtene som påvirker feilene. Feil kan føre til misnøye hos kundene, noe som kan føre til redusert salgsvolum. Effektanalyse refererer til å studere konsekvensene eller årsakene til disse feilene. Derfor er formålet med FMEA å ta nødvendige tiltak / skritt for å eliminere eller redusere feil, med utgangspunkt i de som har høyest prioritet.
FMEA brukes på designfasen for å forhindre feil. Deretter brukes den i kontrollfasen, før og under pågående prosessdrift. FMEA bør startes i de tidligste konseptuelle stadier av design og må fortsette gjennom hele produktets eller tjenestens levetid.
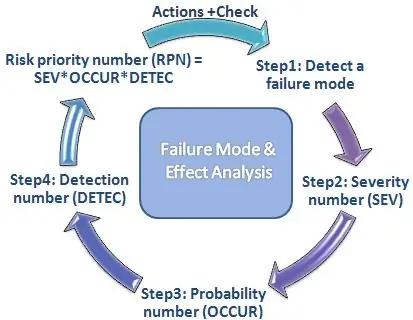
FMEA kan brukes i,
• Designe eller redesigne prosessen, produktet eller tjenesten etter distribusjonen av kvalitetsfunksjonen.
• Når du utvikler et produkt med flere funksjoner.
• Før du utvikler kontrollplaner for en ny prosess.
• På tidspunktet for forbedring planlegges mål for en eksisterende prosess, produkt eller tjeneste.
• Analyse av feil i en eksisterende prosess, produkt eller tjeneste.
Hva er FMECA?
FMECA er en forbedret versjon av FMEA ved å legge til en kritisk analyse-seksjon, som brukes til å kartlegge sannsynligheten for feilmodus mot virkningen av konsekvensene. FMECA kan illustreres som en metode som brukes til å identifisere systemfeil, årsakene bak feilene og virkningen av disse feilene. Med begrepet Criticality kan FMECA-prosessen brukes til å identifisere og fokusere på designområdene med stor bekymring.
Videre kan FMECA være nyttig for å forbedre utformingen av produkter og prosesser, noe som vil gi høyere pålitelighet, økt sikkerhet, bedre kvalitet, kostnadsreduksjon og økt kundetilfredshet. Dette verktøyet vil være nyttig når du oppretter og optimaliserer vedlikeholdsplanene for reparerbare systemer og andre kvalitetssikringsprosedyrer.
I tillegg kreves både FMEA og FMECA for å oppfylle kravene til kvalitet og sikkerhet, som ISO 9001, Six Sigma, Good Manufacturing Practices (GMPs), Process Safety Management Act, etc.
Hva er forskjellen mellom FMEA og FMECA?
• FMEA-metoden gir bare kvalitativ informasjon mens FMECA gir både kvalitativ og kvantitativ informasjon, som gir muligheten til å måle ettersom den knytter et kritisk nivå til feilmodus.
• FMECA er en utvidelse av FMEA. Derfor, for å utføre FMECA, er det nødvendig å utføre FMEA etterfulgt av kritisk analyse.
• FMEA bestemmer feilmodusene for et produkt eller prosess og deres effekter, mens Criticality Analysis rangerer disse feilmodusene i rekkefølge etter viktighet ved å vurdere feilprosenten.